Our History
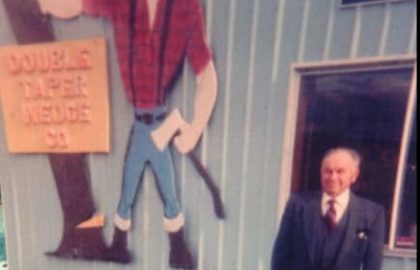
Jacob Piller circa 1975
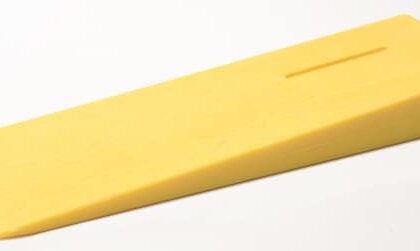
Felling Wedge
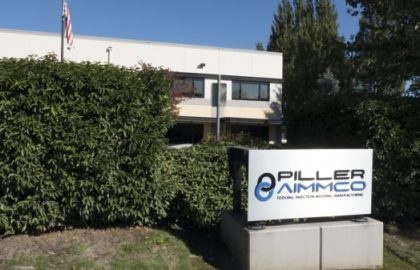
PILLER AIMMCO Molding 2016
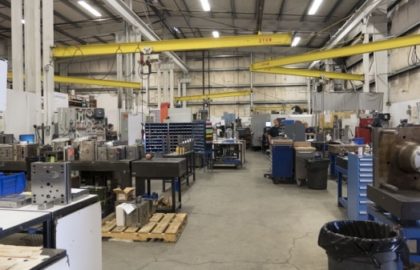
PILLER AIMMCO Tooling Shop Floor
Our roots in injection molding are deep, dating back to 1963 when our founder, Jacob Piller, introduced an innovative injection molded plastic tree felling wedge to local Pacific Northwest woodsmen. Inexpensive, light weight and tough, Jacob’s patented design was quickly adopted by the logging industry, and continues to be produced today in a multitude of sizes and configurations that are distributed world-wide.
In the ensuing years, Piller Plastics became recognized as a premier regional custom injection molding operation. Continually investing in people, processes and equipment, and with a sharp focus on providing clients exceptional personalized service, we grew together with the regional economy delivering injection molded components to OEM’s such as Epson, Panasonic & Mattel.
In late in 2014, Piller Plastics merged with AIMMCO, a successful tooling & injection molding company with a reputation for exceptional service, innovation, and product development prowess.
The resulting vertical integration of our combined organization offers clients a very unique value proposition with full development and production capabilities from part design & tooling to high volume production and turn-key integration.
TODAY
Our operations feature in-house engineering, design & tool construction with a staff of nine mechanical engineers driving the process. Product development activities are accomplished outside the production environment on dedicated molding presses supported by an accomplished technical staff operating 3-shifts to quickly effect mold changes and product iterations.
Production injection molding is carried-out in our 55,000 sq. ft. facility on 45 molding presses, including high-speed, vertical and two-shot, ranging in tonnage from 35 to 1,200. Robotic automation together with automated drying & feed stock blending, including color and regrind addition is used for high volume production, while short run low-volume jobs are given the same care and attention required to meet quality, cost and delivery objectives.