Mold Types
At PILLER AIMMCO, we design & construct a range of mold types, working with clients to fully understand their production needs, lead times and budgets, whether high volume production with multiple cavities, family type tools, or low volume molds intended for testing and prototype development.
Multi Cavity Tool
We have extensive experience incorporating hot manifolds and 3-plate systems as well working through the nuanced details required to successfully produce complex geometries such as reverse ejection systems, actuated & timed slides & lifters, collapsing cores, unscrewing mechanisms, air blast assisted and sequenced ejection, and bench cores just to name a few.
SPI Mold Classifications
When evaluating tooling offerings from various sources, one is often faced with the challenge of comparing apples to oranges. There are a range of mold materials, design & construction details and accessories that directly affect mold price and performance, so unless one is well versed in these nuances it can be extremely difficult to compare competitive offerings. For this reason the Society of the Plastics Industry (SPI) established mold standards and classifications back in the late 1970’s to provide guidance for purchasers, and to level the playing field for the tool making industry. These standards, revised several times since, are still widely used as references in RFQ’s to compare competitive offerings, and to specify minimum levels of tool construction to meet production objectives.
That said, the SPI mold classifications are not intended to serve as design standards, nor do they relate to part design & material nuances that will dictate a particular tooling approach such as gating, runner systems & specific materials of construction. They also do not constitute a guarantee or imply any level of quality or workmanship, so in order to launch a successful injection molding project it is of upmost importance to engage and partner with experienced mold makers that can collaborate and guide clients through the process. Having produced thousands of injection molds with requirements ranging from tight budgets and a few development parts, to complex multi-cavity high volume production, PILLER AIMMCO is proud to be the trusted partner of clients spanning a diverse range of industries.
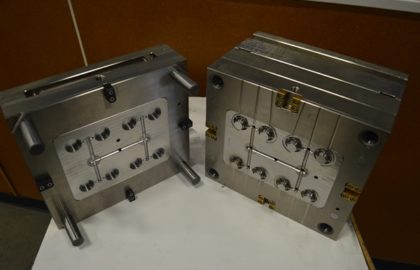
SPI Class 102, Eight-Cavity Injection Mold
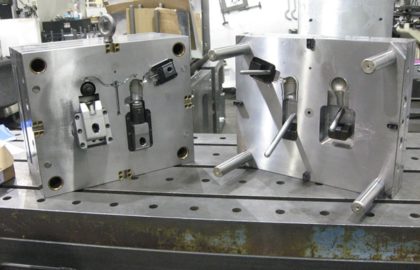
SPI Class 103, Two-Cavity Family Injection Mold with Three Slides
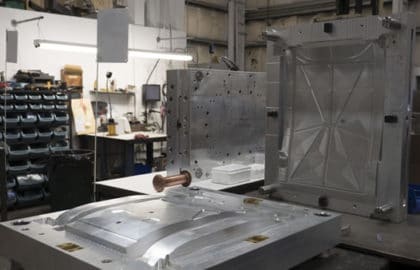
SPI Class 104, Single Cavity Aluminum Prototype Injection Mold
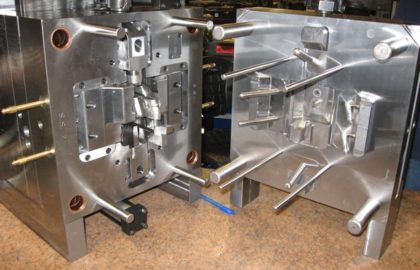
SPI Class 103 Injection Mold with Four Slides & Lift Bar
Following is a brief overview of the various SPI mold classifications including descriptions for each mold class. The full document can be obtained through SPI
CLASSIFICATIONS OF INJECTION MOLDS UP TO 400 TONS
General Notes
* Mold life cannot be guaranteed due to variations in part design and molding conditions. This guide provides approximate cycles for each type of mold and in no way constitutes a warranty or guarantee.
CLASS 101 MOLD
*Cycles: One million or more
Description: Built for extremely high production. This is the highest-priced mold and is made with only the highest quality materials.
Detail:
1. Detailed mold design
2. Mold base minimum hardness of 280 BHN
3. Molding surfaces (cavities and cores) hardened to a minimum of 48 R/C range. All other details, such as slides, heel blocks, gibs, wedge blocks, etc. hardened tool steels
4. Guided ejection
5. Wear plates on slides
6. Temperature control provisions wherever possible
7. Plates or inserts containing cooling channels of a corrosive resistant material or treated to prevent corrosion
8. Parting line locks are required on all molds
CLASS 102 MOLD
*Cycles: Not exceeding one million
Description: Medium to high production mold, good for abrasive materials and/or parts requiring close tolerances. This is a high quality, fairly high-priced mold.
Detail:
1. Detailed mold design
2. Mold base minimum hardness of 280 BHN.
3. Molding surfaces hardened to a 48 R/C range. All other functional details made and heat treated
4. Temperature control provisions directly in the cavities, cores, and slides wherever possible
5. Parting line locks
6. The following items may or may not be required depending on the ultimate production quantities anticipated:
a. Guided Ejection
b. Slide Wear Plates
c. Corrosive Resistant Temperature Control Channels
d. Plated Cavities
CLASS 103 MOLD
*Cycles: Under 500,000
Description: Medium production mold. This is a very popular mold for low to medium production needs. Most common price range.
1. Detailed mold design
2. Mold base minimum hardness of 165 BHN
3. Cavity and cores 280 BHN or higher
4. All other extras are optional
CLASS 104 MOLD
*Cycles: Under 100,000
Description: Low production mold. Used only for limited production preferably with nonabrasive materials. Low to moderate price range.
1. Mold design
2. Mold base of mild steel or aluminum
3. Cavities of aluminum, mild steel or any other agreed upon metal
4. All other extras are optional
CLASS 105 MOLD
*Cycles: Not exceeding 500
Description: Prototype only. This mold will be constructed in the least expensive manner possible to product a very limited quantity of prototype parts.
May be constructed from cast material or epoxy or any other material offering sufficient strength to produce minimum prototype pieces.
CLASS I UNIT INSERT**
*Cycles: Approximately 500,000
Description: Top quality materials for medium to high production requirements.
CLASS II UNIT INSERT**
*Cycles: Under 100,000
Description: Similar to Class 104 Mold. Most commonly used insert. Low to medium production.
CLASS III UNIT INSERT**
*Cycles: Less than 500
Description: Similar to Class 105 Mold. Least expensive insert for very limited quantities. Insert built with the lease expensive materials.
* Cycles are approximate and for comparison only.
CLASS 1 UNIT INSERT
1. Detailed mold design required
2. Insert retainer to be uniform hardness of at least 280 BHN
3. All molding and/or functional details made of tool steel hardened to at least 48 R/C
4. Slides have wear plates
5. Temperature control provisions in cavities, cores and slides wherever possible
6. Plates or inserts containing cooling channels be of a corrosive resistant material or treated to prevent corrosion
7. Parting line locks
8. Insert retainers have leader pins and bushings or some similar guidance system
CLASS II UNIT INSERT
1. Detailed mold design
2. Insert retainer uniform hardness of at least 165 BHN
3. Cavities and cores m 280 BHN or higher
4. Water channels included
5. All other extras are optional
CLASS III UNIT INSERT
Can be constructed from aluminum, cast metal, cast epoxy or any material with sufficient strength to produce minimum prototype parts